Rivets may not be the most noticeable component of a bag, but they play an important role. Upon inspecting my bag, I counted at least 12 rivets. Eight of them are placed strategically in areas prone to stress or friction, such as where the straps attach to the main body of the handbag. The other four rivets are purely for decoration, positioned at the spots where the pockets stitch onto the material, giving a stylish look to the bag.
Let’s talk about something practical instead of focusing on stylish looks. Rivets are not the first thing that comes to mind when we think of handbags, but they are essential. These little details can reinforce our favorite handbags, ensuring they are durable and long-lasting. Rivets are like the unsung heroes, quietly adding strength where we need it most, preventing those dreaded tears and frays. However, not every handbag flaunts these sturdy studs. It all boils down to the design and purpose behind each bag, whether a casual carry-all or a chic statement piece.
Let’s dive into the world of rivets and discover why they’re important bag components. Rivets – Everything You Need To Know!
Riveting Rivets, Wonderful! What Are They Exactly?
The short answer: Rivets are fasteners used to combine two or three pieces of material.
The long answer: Rivets, those small yet mighty fasteners, play an important role not only in fashion. They add style and strength to handbags and belts in various industries like automotive and electronics manufacturing. Where they’re used to assemble cars and secure delicate components, with their tail-and-head design, these cylindrical wonders create a lasting bond between materials—ensuring durability and reliability in everything from our favorite accessories to our vehicles. So, whether you’re admiring a sleek handbag or marveling at the engineering of a car, remember to tip your hat to the unsung hero—the rivet.
History and Evolution of Rivets
Riveting, a cornerstone of iron and steel structures, traces its origins to the early boiler-making and shipbuilding industries. Industries initially adopted it as a joining technique. Still, it quickly found its application across various domains, including civil engineering and the construction of public and private buildings. As the Industrial Revolution progressed, riveting techniques improved significantly, leading to advancements in both design and application. Riveting enjoyed its heyday in the 19th century before the 20th century saw a gradual shift toward electric arc welding. Despite this shift, riveting’s legacy endures, especially in heritage architecture. Interestingly, it also continues to play a crucial role in manufacturing bags. It was contributing to the creation of durable and stylish products.
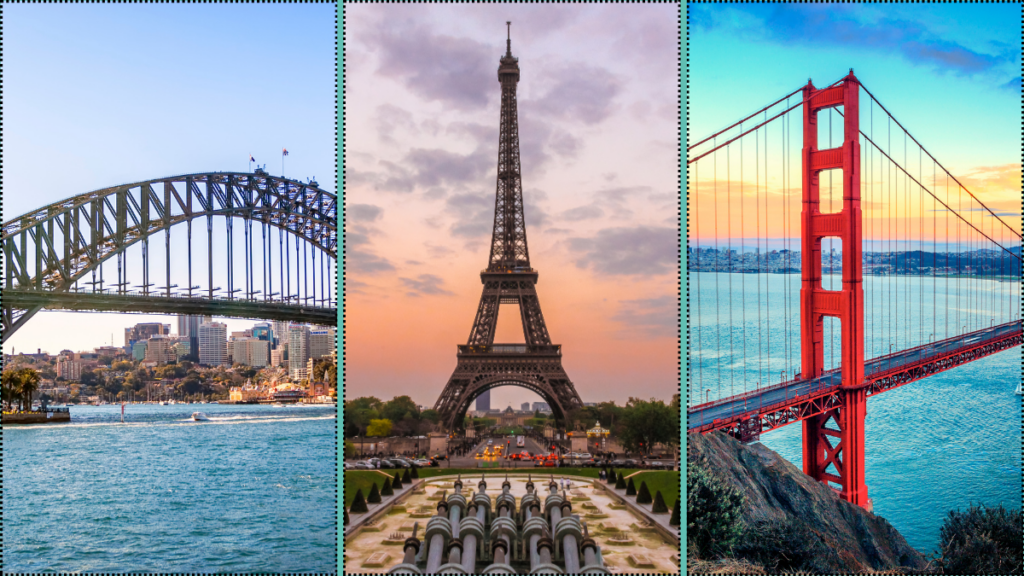
Civil Engineering
Rivets play a pivotal role in constructing iconic structures around the globe, ensuring their strength, stability, and durability. Over six million rivets were used in the 1930s to build the Sydney Harbour Bridge. A symbol of Australia’s engineering excellence, showcasing the meticulous effort of riveters. Meanwhile, approximately 1.2 million rivets hold together the Golden Gate Bridge, a symbolic suspension bridge completed in 1937 in San Francisco. Standing strong against the region’s challenging weather and seismic conditions. Additionally, the Eiffel Tower, a masterpiece of wrought iron architecture erected for the 1889 Exposition Universelle in Paris, incorporates an estimated 2.5 million rivets, contributing to its resilience and enduring status as a cultural icon. These examples highlight rivets’ critical and often overlooked role in constructing monumental structures that continue to captivate and inspire.
Materials Used
Like other fasteners such as zippers, manufacturers mainly use metals and plastics to make these important components.
In the evolving landscape of bag manufacturing, manufacturers have notably diversified the selection of materials for rivets. They have moved beyond traditional choices to include innovative materials like aluminum, zinc-coated steel, brass, stainless steel, and now, other metal materials and even plastics to cater to specific product types and needs. With its robustness and aesthetic appeal, brass has become the preferred material for leather products. Its compatibility with the luxurious and durable nature of leather goods ensures that items such as high-end handbags, belts, and wallets exhibit enhanced visual appeal and maintain structural integrity over time. The choice of brass in leather products underscores a commitment to quality and longevity, reflecting the premium market segment these items often occupy.
Durability and Design
Meanwhile, suitcase manufacturers have favored stainless steel for its superior strength and resistance to corrosion. This material is particularly suited for suitcases, which must be durable enough to withstand the rigors of travel. The resilience of stainless steel ensures that suitcases retain their functionality and appearance over numerous journeys, making it the preferred choice for brands committed to producing high-quality travel gear.
Strategic Material Selection Balancing, Durability, and Practicality
Manufacturers are also exploring the potential of plastics like nylon and polyethylene in their products. They often choose nylon for its remarkable strength and durability, making it an excellent choice for parts of bags that undergo significant wear and stress. Polyethylene, known for its lightweight and resistance to moisture and chemicals, is particularly useful in creating components that withstand harsh conditions without adding unnecessary weight to the product. This strategic selection of brass for leather products, stainless steel for suitcases, and durable plastics like nylon and polyethylene exemplifies the industry’s nuanced approach to material choice. This strategy aims to optimize the balance between aesthetics, durability, and practicality in line with the specific demands of different product categories.
Advantages
In my journey through bag manufacturing, I’ve come to rely on materials that guarantee both durability and strength. Metal materials, in particular, shine in this role. They ensure that each bag can withstand considerable wear and tear, promising an impressive lifespan due to its robust nature. One must-have for bags exposed to various environments is the ability to resist corrosion, and that’s another aspect I really appreciate. However, plastics hold their special place in the design process. Their lightweight nature is a boon, significantly reducing the overall weight of the bags. They also present a more budget-friendly option compared to metals. Plus, plastics boast excellent corrosion resistance and offer unmatched versatility in manufacturing. This flexibility allows me to explore various shapes and designs without complex processing.
Limitations
Despite their numerous benefits, it’s crucial to understand that metals and plastics have their respective limitations. For all their strengths, metals can significantly increase the weight of a bag, which is a drawback when lightness is a key consideration. Moreover, the cost of premium metals like brass and stainless steel can escalate the overall expenses. Some metals may also require additional processing to enhance their corrosion resistance, complicating their use further. On the other hand, while advantageous in many respects, plastics fall short in durability compared to metals. This difference can affect the longevity of the bags. Environmental concerns also loom large with plastics due to non-biodegradability and recycling challenges. There’s also the potential for bags utilizing plastic components to be perceived as lower quality.
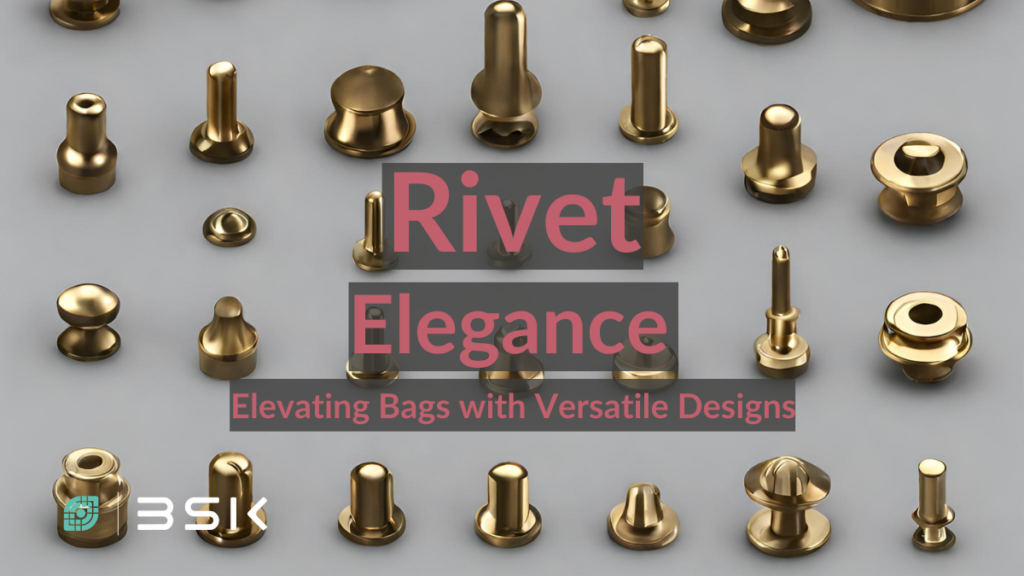
Styles of Rivets
In bag manufacturing, many styles of rivets are used. Here are some of the common types of rivets used:
Double Cap Rivets display a decorative cap on each end, offering a polished look while fastening multiple material layers together. Manufacturers commonly use them in leather bags and accessories for function and aesthetics.
Tubular Rivets, solid with a hollow shaft, add strength and durability to bags. Their design is ideal for applications needing a flush or low-profile finish.
Rapid Rivets, or single-cap rivets, provide a quick and easy installation method. They can attach labels, tags, and decorative elements to bags.
Split Rivets, also known as bifurcated rivets, feature a split end that expands after insertion to secure the rivet. They are useful for fastening hardware like buckles, snaps, and D-rings to bags.
Decorative Rivets, including cone, stud, and rhinestone rivets, introduce style, personality, and visual appeal to bag designs. They can serve as both functional fasteners and decorative accents.
Bag manufacturers commonly use these rivets to provide the finished product with versatility, strength, and aesthetic appeal. The choice of rivet type depends on the material, design, intended use, and desired aesthetic outcome of the bag.
Manufacturing Process
In the manufacturing process of rivets for bags, manufacturers select the appropriate material, such as brass, stainless steel, aluminum, or plastic, for its strength, durability, and corrosion resistance. They then cut the material into the desired length to form the rivet body, ensuring uniformity in size and shape. Depending on the material and design requirements, manufacturers shape these pieces into the desired rivet form using stamping, forging, or machining.
Manufacturers process the shaped rivet bodies to form the head of the rivet through methods like upsetting (compressing) or pulling the material to create the desired head shape. After forming the rivet head, they treat the surfaces of the rivets with processes such as polishing, plating, coating, or painting to enhance their appearance and properties. This includes providing corrosion resistance, improving aesthetics, or adding color. Once the rivets pass the necessary checks, the manufacturers package them and prepare them for shipment to bag manufacturers or suppliers. Each step in this process is crucial for producing high-quality rivets that meet the functional and aesthetic requirements of bags and other leather goods.
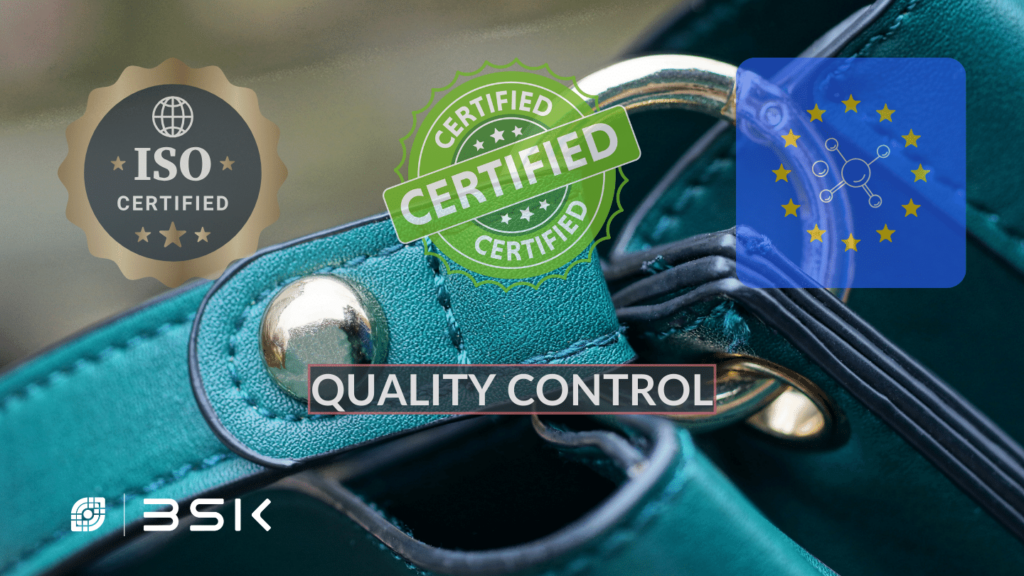
Quality Control
Quality control in rivet manufacturing for bags involves material inspection, dimensional and visual checks, mechanical testing, and surface treatment verification. It ensures rivets meet strict standards, including ISO 9001, ASTM International, and REACH compliance. Production includes detailed documentation for traceability, demonstrating a commitment to high-quality components that satisfy manufacturers and end-users.
Design and Aesthetics
Rivets are essential for both the structure and style of bags. They serve as functional fasteners while enhancing the overall design, adding texture, contrast, and decorative elements. Designers can use unique shapes, finishes, and embellishments to create distinctive focal points that reflect the brand’s style and craftsmanship. Rivets can also be strategically placed to create visual interest or highlight specific features of the bag. Overall, rivets contribute to the bag’s aesthetic appeal and are integral to creating visually captivating and aesthetically pleasing bags.
Conclusion
Rivets play a crucial role in enhancing both the durability and aesthetic appeal of bags, with their strategic placement being key to achieving both strength and style. Their significance extends beyond just fashion, underscoring their versatility. In the realm of bag manufacturing, rivets are particularly valued for their ability to contribute to both the longevity and visual appeal of products. With a rich history of industrial innovation, rivets are integral to creating iconic designs, often utilizing materials like brass for their robustness and aesthetic appeal. It’s beneficial for manufacturers to explore alternative rivet materials and applications, aiming to optimize the functionality and design of their products. If you’re not sure or have inquiries into the possibility of producing bags, why not get in touch with us here at BSK Fashion? We are happy to help, from development to production.